Last Updated on July 28, 2021
Threaded fasteners of many types have been developed over centuries and are generally used to hold two or more parts together. In this article we will include pretty much all types of metal fasteners under the single term, bolt.
If all goes well in a lifetime, every bolt needed to be removed simply comes out with moderate coaxing. Unfortunately, there can be trying moments. In such moments a formerly-cooperative bolt can refuse to unscrew.
Here we will discuss why this can happen and what to do about it.
What Conditions Make Some Bolts Difficult to Remove?
Stripped Bolt
This bolt was probably over-tightened (over-torqued). The threads of the bolt, or the threads of the associated hole where it is installed have stripped away. Or there may be a stripped nut hindering bolt removal. The fastener can be turned but it won’t come out.
Rusted Bolt
This bolt is probably part of a corroded assembly such as parts of the exhaust system. The rust process has seized the bolt in place. It cannot be rotated using normal means.
See Also: Symptoms of a Hole in Your Exhaust
Rounded Off Bolt
Sometimes, a removal attempt has rounded off the wrench flats. Usually this happens when using the wrong size wrench or socket. A good socket set (and wrench set) is something almost every garage should have.
Rounded off oil drain plugs seem to be too common of an occurrence. Usually this happens because a person can’t find the correct size socket so they use the next closest.
Broken Bolt Head
Often, the worst case is when the bolt head has broken off and you are looking at a rusty cylindrical pin. If you’re lucky, there will be enough threads showing to allow removal.
What Situation Makes it Nearly Impossible to Remove a Seized Bolt?
A seized bolt can be impossible to remove when access to it is extremely difficult. An example of this might be a fastener for a starter motor located down between the side of the engine and the fender of your car.
You might just barely be able to get a wrench or socket on this bolt. And it either turns freely (it’s stripped) or it won’t turn at all (it’s seized). And the bolt head is now rounded off from your struggling to get it out.
If it was difficult to get near this bolt with a wrench, you are probably not going to be able to get near it to remove it using the methods described in this article. In this case, you will have to get the vehicle to a skilled technician for corrective action.
But if you have good access to any offending bolt, the techniques below and some sweat may enable its removal.
How to Remove a Stripped Bolt (Best Method)
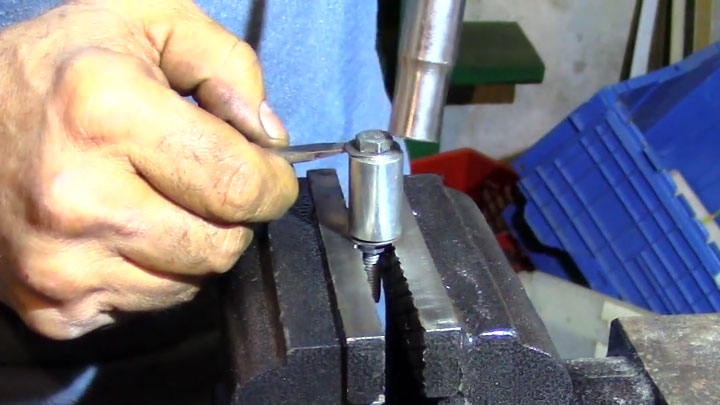
Typically a stripped bolt can be turned, but it won’t come out. If this is the case, the bolt can be pried out. Here’s how this can be done.
A sharpened screwdriver or small chisel will be required. Place the tool blade at the point where the bolt head meets the adjacent part surface. Using a hammer, tap the sharpened blade into the gap between the bolt head and part.
As you tap, the bolt should begin to back out of the hole. You may have to move your tool point to the opposite side of the bolt head and repeat this action several times. Do not strike the tool too hard as this can break off the bolt head.
When a gap has opened, you should spray some WD-40 (or equivalent thin penetrating oil) into the gap to help lubricate the bolt in its hole. Turning the bolt after applying the oil will spread the lubricant and help ease the next step. If the bolt refuses to turn easily, a couple of WD-40 applications with a five minute wait between treatments can help loosen it.
You may need to open the gap more fully to get the bolt to turn freely. In this case, insert a larger screwdriver blade into the gap and attempt to pry the bolt further out. It should begin to move. If you are successful, the bolt may now be sufficiently loosened so that you can grab it with vise-grip pliers, rotate it and pull it free.
How to Remove a Rusted or Rounded Off Bolt (4 Methods)
A rusted or rounded off bolt, seized in place, will be far more difficult to remove than the stripped bolt discussed above.
Often steel bolts installed in a cast iron or aluminum engine block can become sufficiently corroded that removal is extremely difficult. The corrosion process combined with galvanic effects causes the bolt and threaded hole material to chemically bond to one another.
The removal techniques discussed below all attempt to fracture the chemical bond and free the bolt. If the bolt head remains in good hexagonal form and condition, a standard wrench or socket should be adequate to turn it.
In general, a 6-point socket will prove best for this purpose. A 12-point socket grabs the high points of the bolt head and can more quickly round it off when it is seized in place. If you’re looking for a good socket set, it’s hard to do better than DeWalt’s 192-Piece set at its price point.
If the bolt head is rounded off, the head is broken off, or the fastener is a stud and has no head, an alternate means of gripping it will be required. Most of these gripping and removal methods are not equal to having the head in good shape, but each can get a bolt out.
#1 – Vise Grip Pliers
Grip the head or bolt shank with a pair of vise grip pliers. Larger vise grips work better than smaller ones because they can exert more grasping power. Plus you will have better leverage with a longer tool.
Do be aware when using vise grips that they may tend to slip off the bolt which can gradually wear it away or reduce its diameter, and it may break off.
On larger bolts, grinding or filing a pair of flats opposite one another on the bolt shank can provide a better gripping surface for the vise grips.
If space permits a pipe wrench can be used instead of vise grips to grab and turn the bolt.
#2 – Rotary Tool
Use a rotary tool (ie: Dremel tool) with a thin grinding wheel to make a straight groove across the top of the bolt. This groove should be wide enough and about 1/8″ deep so you can use a large screwdriver to attempt to turn the bolt.
Square shank screwdrivers (or a screwdriver with hex flats near the handle) work best for this because you can use an open end wrench on the screwdriver shank to increase your turning power.
#3 – Bolt Extractor
A very effective way to grip a damaged bolt, nut or stud is by using an external bolt extractor tool. Quality manufacturers such as Irwin offer such devices at reasonable cost. These sockets have internal spiral teeth with a slight internal taper and are made of high strength steel.
Fitted onto a rounded off bolt head or broken off stud, the extractor must be hammered firmly into place. Then it can be turned using a conventional 3/8″ or 1/2″ drive ratchet or breaker bar.
Gradually increase the torque applied to the bolt to avoid spinning the grip socket on the bolt and rounding it off.
#4 – Two Nut Method (if Bolt Head is Missing)
If the bolt head is missing, but threads are present and in reasonable condition, this technique can sometimes work. Clean the threads with a fine wire brush. Coat the threads with Loctite Threadlocker 262.
Install two nuts on the end of the bolt and tighten them against one another as tightly as possible using two open end wrenches.
Allow the Loctite to fully set per the manufacturer’s instructions. Having the new wrench surfaces may enable gripping and loosening the corroded bolt with a conventional socket wrench.
A variant of this technique would be to weld a nut on the end of the bolt or stud. Of course, a light duty arc welder and some welding talent is needed to take this step.
Related: Best Way to Remove a Stuck Lug Nut or Lug Bolt
4 Ways to Prepare a Bolt for Removal
Some additional preparational steps can help loosen a rusted bolt before you ever put a wrench on it.
Heat
Using a hand-held propane torch with a fine tip, heat the stubborn bolt for several minutes. By expanding the connected parts, heating can fracture the corrosion bond between the bolt and surrounding metal.
Apply torque to remove the bolt as discussed above as soon as you remove the heat from the area.
In particular, you must avoid rubber or plastic fuel lines and brake hoses which can be burnt through in an instant with disastrous results. Always have a fire extinguisher (Class A:B:C minimum) immediately accessible when using open flames for any purpose in your garage and around your automobile.
Impact
Use a ball peen hammer to strike the exposed end of the bolt. Hit it sharply several times. Such impact can break the corrosion bond that is preventing the bolt from being loosened. Then attempt bolt removal as described above.
Impact Wrench
If sufficient bolt head is present, attempt removal using an impact wrench instead of a socket wrench. The applied impact can often break free an otherwise frozen bolt.
Note however that the power of an impact wrench on a worn bolt head may spin the socket without turning the bolt and further round the head away.
Lubricant
Where the bolt enters its mating part, soak the metal with WD-40 or an equivalent penetrating oil. Allow it to set overnight. For some corroded fastener situations, the oil will penetrate and help ease the force required for removal.